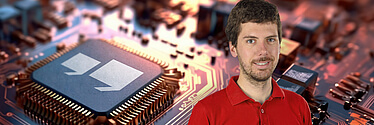
Long-term Approach to the Component Shortage
Impact of the Chip Shortage on the Energy Industry
Whether you wanted to buy a new car, build a house, or get hold of a game console to fill the hours during the lockdowns – since the beginning of 2021, we have all been feeling the effects of the chip shortage on the global economy. It goes without saying that the crisis has also impacted the energy sector. Limited availability, astronomical prices, and unreliable delivery times meant we too faced challenges on a scale we had never seen before. Today, our delivery times have returned to their pre-crisis level. In this article we have summarized how we achieved this and what it means for future orders.
The wide-ranging effects of the shortfall – causes and consequences of the component shortage
The causes of the component crisis were and still are varied. They can be attributed partly to the coronavirus pandemic and are partly influenced by other global and sociopolitical events, leading to a complex situation.
- Lockdowns restricted production enormously in many places.
- The significant increase in demand for home entertainment equipment and home office equipment resulted in a huge demand for semiconductor components.
- Passenger transport came to a standstill during the international lockdowns further restricting freight capacity and causing shipping costs to rise.
- The conflict between Russia and Ukraine further intensified supply chain challenges in certain sectors by restricting deliveries of metals, food, chemicals, and other raw materials.
- The increasing popularity of electric cars is also affecting the availability of components, as these vehicles require considerably more electronic components than those with combustion engines.
The consequences were uncertain and unreliable delivery times and a price increase of over 400%. We were forced to procure components via new channels, which – in addition to astronomical price ranges – also introduced a quality risk, resulting in additional quality assurance tests having to be performed on every delivery.
Optimizing delivery times & a sustainable approach to the shortage
It was clear to us from the beginning that we had to meet this challenge with a long-term approach that would also deliver quick solutions, fulfill our customers' requirements, and guarantee consistent quality.
To meet these high demands, we established an interdisciplinary Shortfall Panel. The aim of the panel was to monitor the situation, make decisions about certain critical orders and tenders, enable additional delivery time optimizations, and ensure prompt and seamless communication with our customers and sales partners.
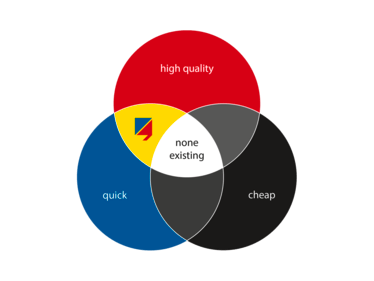
"It was clear that we needed quick yet reliable solutions, and they would only be possible with a high level of investment."
– Johannes Malin, Shortfall Panel Lead, OMICRON
Goals: Reduce delivery times and ensure quality
The Shortfall Panel's objective was clear: keeping delivery times as short as possible without compromising quality. Several measures were introduced for this purpose:
Boosting stock
The first and most obvious step was stocking up on all components and spare parts. We had a considerable advantage over many other companies in this respect, as we have longstanding partnerships with our electronic component distributors and often work directly with manufacturers. In addition, we procure a significant proportion of our mechanical components and accessories from regional manufacturers, which limited the effect of global bottlenecks and transport problems to some extent.
We bought components that were unavailable from our distributors or had delivery times that were too long for us in other buying markets, sometimes at much higher prices. These components underwent intensive quality testing before being used in series production, helping us remain in a position to supply our products.
At the same time, we invested in 21,000m2 (226042.12ft²) of additional warehousing space to create more storage capacity.
Order-specific needs assessment
Despite increasing our stock, we were also affected by shortages, which required us to improve delivery times and assess and prioritize orders. The Shortfall Panel developed a process that enabled us to work on special orders with a higher priority, such as in emergencies after natural disasters or for system-relevant applications.
Seamless, transparent communication with customers and sales partners
Communication with our customers and sales partners regarding delivery times was just as crucial. Remaining in close contact with them enabled us to understand and respond to their individual needs and manage their expectations. This made it possible to provide realistic delivery estimates and keep our promises.
Long-term supply security
In addition to quickly reducing delivery times, we also wanted to minimize potential long-term delay issues. To this end, we analyzed and optimized production processes.
A dedicated team was assigned the task of looking for alternatives for components that were difficult to get hold of and proactively overhauling our products, making it possible to use different components while achieving the same level of quality and functionality. More common components found their way into our products. This step should ensure availability even in the event of challenging market situations in the future.
Successfully normalizing delivery times
Thanks to the joint effort of all the teams involved and large investments in both time and money, delivery times have been steadily reduced, and over 95% of our products are now delivered within the pre-crisis time frame of four weeks or less.